How Do New Products Come to Market?
- Sparrow Production works on costing, packaging, new molds, and more.
- The VP of Sales Advantus and VP Creative Director of Sparrow present new items to Michaels.
- The Buyer will verbally select new items.
- Once items have been selected, the New Item Form (NIF) and Item Quote Sheets (IQS) are created by Sparrow.
Process
- Sales Ops receives the IQS spreadsheet from Sparrow and fills in the appropriate information.Β
- Melissa/Sparrow will submit the IQS forms to the MIK Merch/Sourcing Teams, who will then upload them into Michael’s SPEDY system.
- Product & Sourcing Specialist receives the NIF from Sparrow and fills in the appropriate information, which will be entered into Net Suite.
- NOTE: UPCs, GTINs, and SKU numbers are generated by Michaels and are available when the items are finalized in SPEDY.
- After the IQS are uploaded into SPEDY, Product & Sourcing will verify when items are listed in the SPEDY portion of MIK’s Vendor Connect and download the “Completed Import Item” report.
- See SPEDY Completed Import Item for the process.
- P&S will review all the information against the NIF and advise Sparrow of any discrepancies.
- NOTE: It can take up to 2-3 weeks from IQS upload to the SPEDY report to be ready for review.Β
- There are no notifications. P&S needs to keep checking weekly.
- Product & Sourcing SPEDY Item Info Report:
- Ensure the description, inner pack quantities, master pack quantities, and cost match what was on the NIF/in ADV system.
- Pull UPCs and SKU #’s from the SPEDY report.
- Β *very important* these link the Advantus item numbers to Michaels item numbers in NetSuite for POs and reports.
- Email SPEDY Info to Melissa, Amy, and Yolanda @ Sparrow. If there are any discrepancies, let them know and have Sparrow confirm what is correct.
- After SPEDY info is confirmed, the Product & Sourcing Specialist will email the Sulyn group (Sparrow, Sales Ops, Product Compliance, DI Purchasing, and C&H Director) the following information:
- NetSuite project information, including the final NIF form.
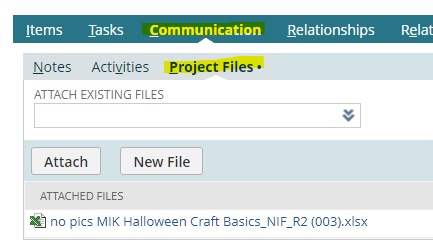
- The email will let various departments know it is their turn in the process.
- Product Compliance- testing will be coming.
- DI Purchasing – know to look for POs.
- C&H Director – to submit customer pricing to Sales Ops.
- NOTE: After this email is sent out, any changes should be made by the appropriate department.
- ex: List price changes by Sales Ops
- Product & Sourcing to add the Factory associated with each new item into the MiPCS portion of MIK’s Vendor Connect NOTE: This can only be done once items are added into SPEDY.
- See Factory Association for DI Items for the process.
- DI Purchasing will receive the Customer PO via EDI
- Types of Orders
- Regular Replenishment/SBA Orders
- DI Purchasing will always review these orders and question if any quantities look weird.
- Contact Laura/Melissa if quantities look off, if they do not meet the MOQ, or if there are any pricing issues.
- Seasonal Orders
- You can tell if a PO is seasonal because it will have event codes on them and seasonal symbols. It may ship to multiple Distribution Centers (DCs).
- Regular Replenishment/SBA Orders
- Types of Orders
- DI Purchasing receives the EDI NetSuite order and compares it against MIC’s original sales order. They must match exactly, then approve the Sales Order in NetSuite. If they do not match, Melissa @ Sparrow must be informed.
- For New or Seasonal Items
- DI Purchasing should immediately notify and email a copy of the Sales Order to Melissa and Laura G, letting them know if it does not match the commitment.
- An alert will notify Product Compliance at this time of items with no previous orders (new items).
- Product Compliance to begin the testing protocol
- NOTE: A passing test report must be received before the Ship Date.
- Product & Sourcing and Product Compliance will receive a do not ship list email if testing is not completed in time.
- Product Compliance will determine if testing needs to be expedited.
- Once the order has been entered into NetSuite, DI Purchasing will confirm that everything matches precisely as the PO Michaels sent over and the NIF.
- Quantities, Ship Dates, Pricing, Items, Item Descriptions, UPCs, Michaels Sku#, etc.
- NOTE: Product & Sourcing has entered additional information (MIK SKU and UPC & GTINs) for DI Purchasing to confirm matches Michael’s PO.
- If this has not been entered, DI purchasing will need to wait to send the POs until the info has been added.
- DI Purchasing will email the PO to the factories and include in the body of the email that the DC Breakdown will be coming later for Seasonal Items.
- For POs going to CMB β AlwaysΒ send them to Freya & copy Christina, Vicky, and Melissa
- If the PO contains new items or new artwork for existing items, copy Yolanda and Jessica at Sparrow, Product & Sourcing, and Product Compliance.
- For POs going to Ningbo Praise β Always send them to Wency & Libby & copy Pandy and Melissa
- If the PO contains new items or new artwork for existing items, also copy Yolanda and Jessica at Sparrow, Product & Sourcing, and Product Compliance
- For POs going to TD β Always send them to Dennie & Water & copy Melissa
- If the PO contains new items or new artwork for existing items, also copy Yolanda and Jessica at Sparrow, Product & Sourcing, and Product Compliance
- For POs going to CMB β AlwaysΒ send them to Freya & copy Christina, Vicky, and Melissa
- Product & Sourcing to email the DC Breakdown, Seasonal Symbols, and Carton Requirements to the factories β Copy Melissa at Sparrow
- POG Set POs for New SBA Items may also have Event Codes that need to be printed on the Case Cartons.
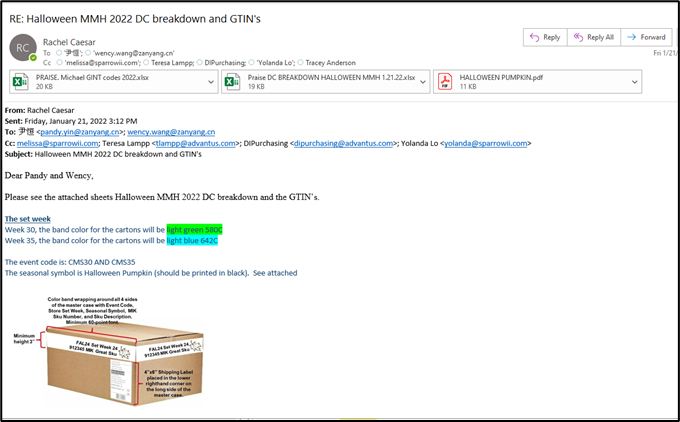
- The Factory will then email DI Purchasing with a PI for Sales Confirmation.
- An alert in NetSuite will notify DI Purchasing if we have not received a PI within 48 hours.
- If this happens, DI Purchasing to contact the Factory for this information.
- DI Purchasing to upload the PI information into the system.
- DI Purchasing to confirm that our PO matches the PI.
- Quantities, Ship Dates, Pricing, Items, Item Descriptions, UPCs, MSI Sku#, etc.
- DI Purchasing to save the PO and PI into the Direct Import Folder.
- DI Purchasing to enter PI receipt date into NetSuite.
- The Product & Sourcing Coordinator will email the Factory three weeks before the ship date for the final packaging dimensions and weights.
- Once received, Product & Sourcing to:
- Mark the dims as verified in NetSuite
- If dims are different, Product & Sourcing to upload to SPEDY via a Fast Sheet spreadsheet.
- See FastSheet Upload for the process.
- If items are assortment/PDQ, they cannot be uploaded into SPEDY. The Fast sheet will need to be emailed to the correct MSI Contact. (Check with Melissa)
- Once received, Product & Sourcing to:
- DI Purchasing is to send a booking reminder four weeks before the ship date.
- DI Purchasing to enter this date into NetSuite.
- The Factory will email the final documents (packing list and commercial invoice) to DI Purchasing.
- DI Purchasing to put final documents into the DI Folder and send them to Direct Import.
- DI Purchasing to enter the received date of the shipping docs into NetSuite.
- DI Purchasing to update NetSuite and the DI Open Tracking Screen with the FCR # and the Cargo Ready Date.
- Once the Seasonal PO ships from the Factory, the Product & Sourcing Specialist will change the status of the items to obsolete and mark the project inactive.
Email Contacts:
Freya β freya.z@chinamutualbenefit.com
Christina β christina.z@chinamutualbenefit.com
Vicky β vicky.h@chinamutualbenefit.com
Melissa β melissa@sparrowii.com
Yolanda β yolanda@sparrowii.com
Amy β amyb@sparrowii.com
Wency β wency.wang@zanyang.cn
Pandy β pandy.yin@zanyang.cn
Libby – libby.liu@zanyang.cn
Water β water@totaldesigninternational.com
Dennie β dennie@totaldesigninternational.com